OUTPUTS
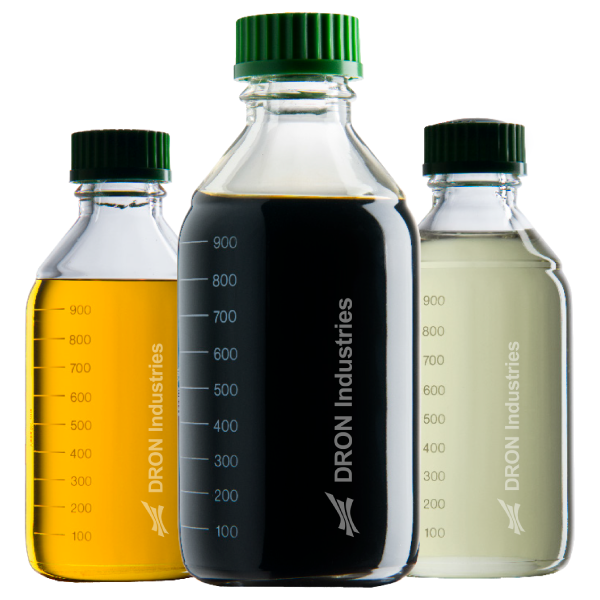
LIQUID FRACTIONS

SOLID FRACTIONS - COKE
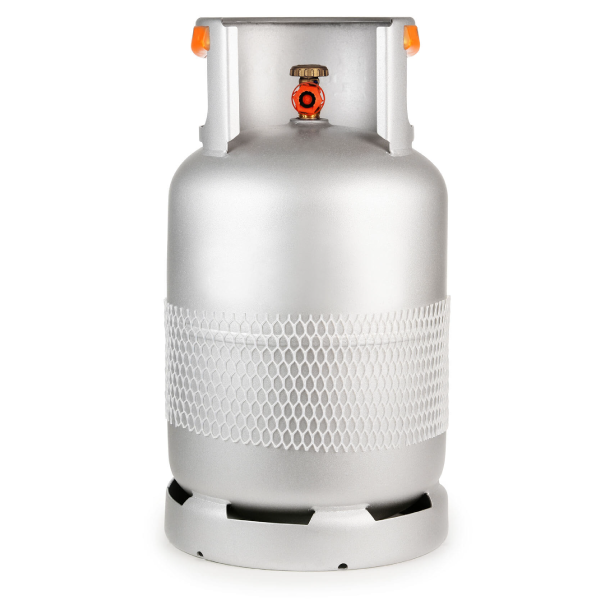
GAS
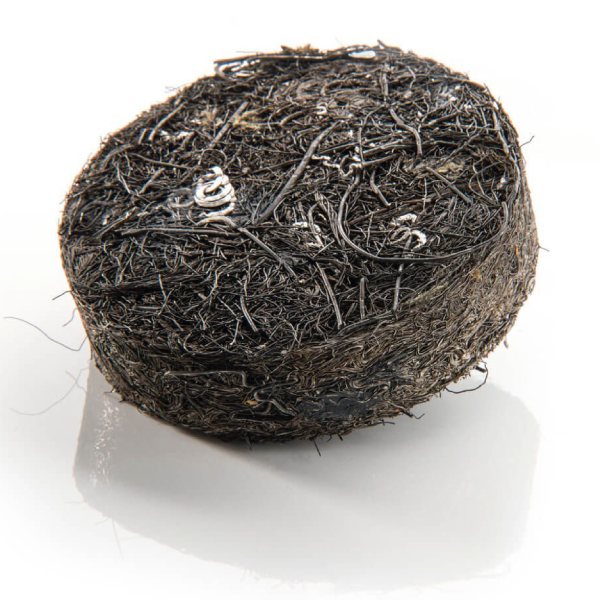
STEEL CORDS
TECHNOLOGY
Deep thermic cracking process - thermal depolymerization is used to process (recycle) the used tires. This is a material recovery (material recycling), where products with 100% yield are obtained. Thermic cracking - thermal depolymerization is based on the use of a flowing-through reactor placed in a furnace, into which crushed tires (cut to approximately 15-25 cm) are continuously dosed. The uniqueness of the device lies in a continuous chemical process that works continuously and the result is the output of the products of the same high quality. For the reactor heating is used its own recycled gas from the process of burning in the gas burners, which are installed in the furnace. The process of deep thermic cracking takes place in an inert (hydrocarbon) atmosphere without the presence of oxygen, i.e. it is not the combustion of material. It is normally operated at a temperature of up to 650 °C. After thermic cracking, the solid residues in the form of carbon and steel cords leave the reactor - in one part. The crackning products in the form of vapours and gas do leave the reactor - in the second part. The vapours do pass through a two-stage condensation system where they do condense to oil. The obtained gas is burned in a controlled manner and replaces external gaseous fuel (normally natural gas or LPG) during operation..
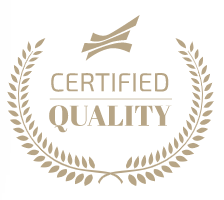
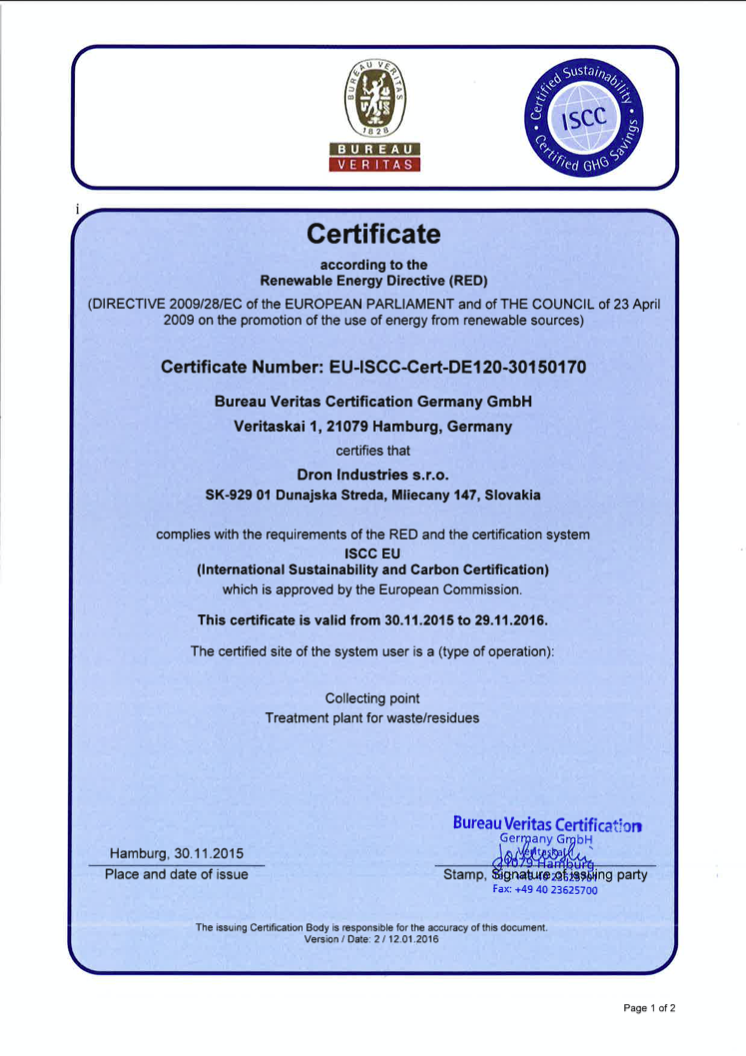
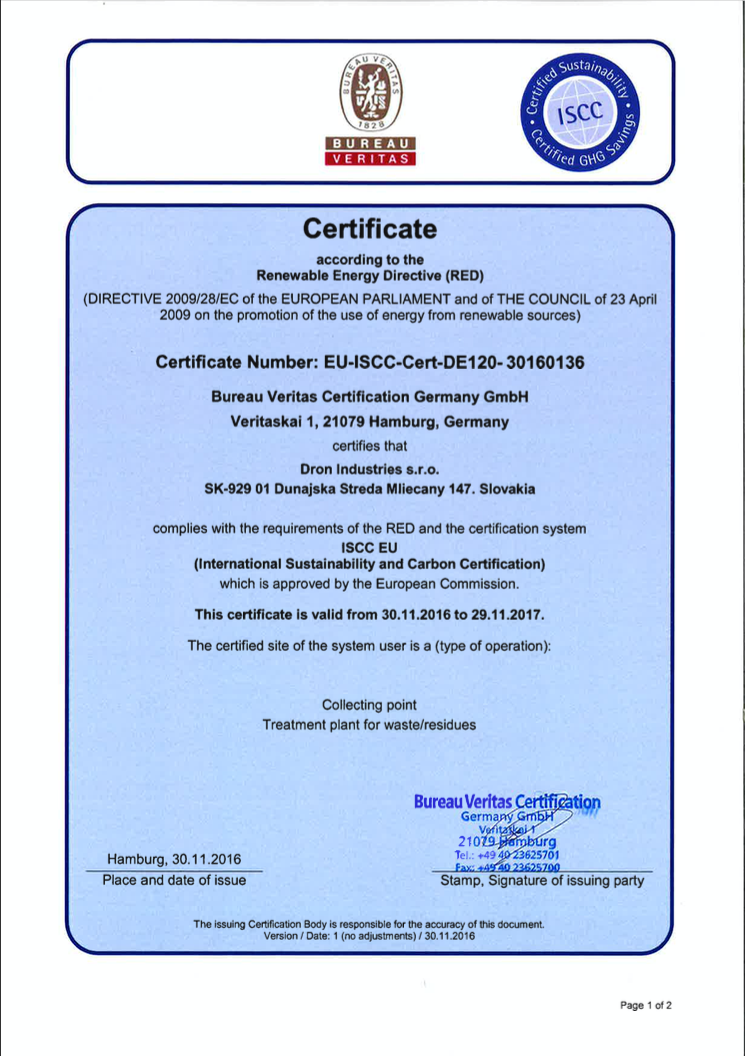
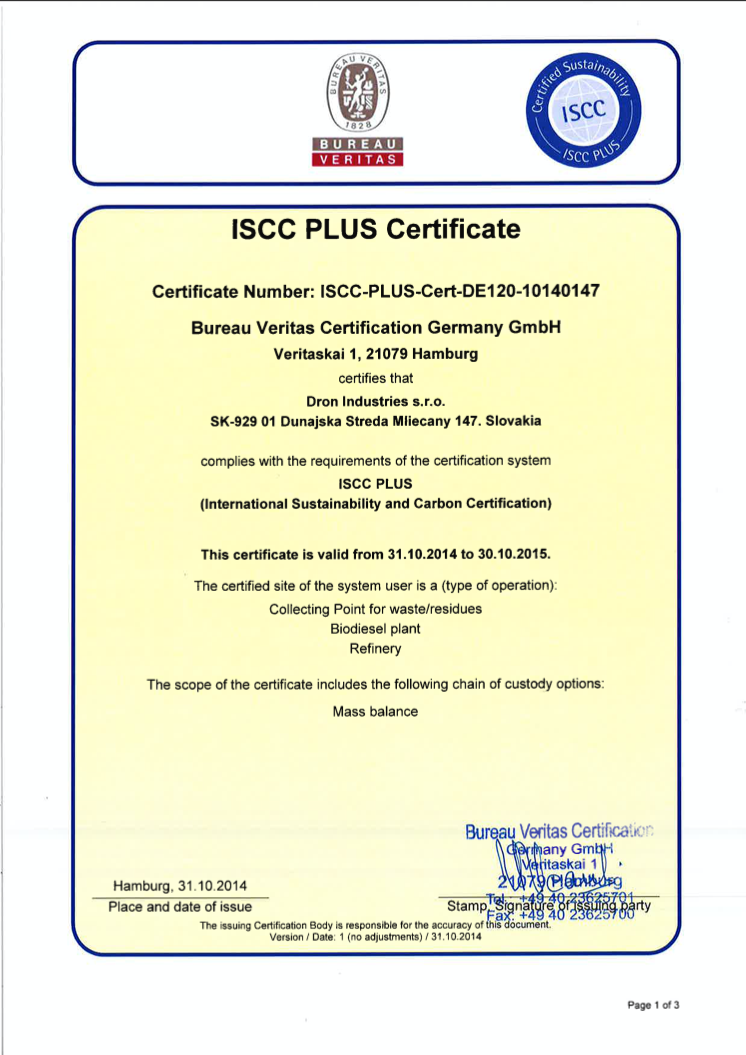